|
Post by skyhawkdon on Mar 14, 2010 20:18:32 GMT 12
sorry mate but there were major delays in the project and the last modified A-4K was only rolled out in 1998............ yes the manufacturing began in the mid !980's but was finished much llater as i belive i will look into this again The first Kahu prototype (NZ6254) flew on 2 June 1988 and the last production airframe (NZ6202) was delivered back to 75 Sqn in June 1991. 21 airframes were upgraded in 3 years, not a bad effort for a small RNZAF/Safe Air team! I'm sure the current C-130 and P-3 upgrade project teams are green with envy!
|
|
|
Post by harvard1041 on Mar 14, 2010 20:43:19 GMT 12
Was on the KAHU Design Team - at AMDF at WB - the prototype flew in 1989 ( 05 ) with the T-Bird ( 54 ) shortly afterwards...exciting times....
|
|
|
Post by Dave Homewood on Mar 14, 2010 21:13:55 GMT 12
The really scary thing is kiwiscanfly wasn't actually born then!!
|
|
|
Post by oj on Mar 15, 2010 20:48:07 GMT 12
Back to Kahu manufacture at PAC: Here is the Armament Control Panel being built up  And here a couple of the finished Armament control Panels and Intercom Control Panels with an armament control relay box and some other box (Don?)  Here is a functional sequence test on an armament relay box.  Here is the Instrument Panel being loomed-up.  And here the full Instrument Panel Frame Assembly.  The Instrument Panel Frame assembly was difficult to build (look at the welding) as it had to be held to very close tolerances and was difficult to inspect dimensionally (Inspectors headache). We had no modern coordinate measuring equipment. That's about all I have to show. If I find anything else in my garage trawl I will of course let you see. OJ
|
|
|
Post by skyhawkdon on Mar 15, 2010 20:58:23 GMT 12
The "other" relay box with the 3 big connectors looks like the System Relay Box, which lived in the nose and did all the switching for the Nav/Attack System. Brilliant photos  The Armament Relay Box was a very compact build - I know it well, as we had to rewire some of it as it was found that Smiths has specified the wrong sized wire for the AGM-65 missile and wires were burning out. This was found during the test flights in 1988/89, so they generated an ECO (Engineering Change Order) for the ARBs to be modified next time they came through the workshop. We were still doing them when I took over the INST/WPNS Bay at Ohakea in 1993! As I have already stated I can't speak highly enough of the workmanship of the PAC team on these boxes.
|
|
|
Post by Bruce on Mar 15, 2010 21:57:39 GMT 12
Makes the Adventurer's wiring seem insignificant! I had to change the warning light fittings in the master warning panel the other day (the lightbulbs kept shaking loose!) and it consists of 3 Lamp bezels (now replaced with LEDs) a test switch and a buzzer - positively primitive compared to this sort of stuff!
|
|
|
Post by b10m on Mar 15, 2010 23:06:09 GMT 12
In the Armament control Panels the AIM 9 switch has off/cool/ and something which I cannot make out, I would imagine a AIM9 would be cool to have, but, I was wondering what the real meaning of cool was?
|
|
|
Post by Barnsey on Mar 15, 2010 23:56:05 GMT 12
It's STBY which we didn't use. Scratching the memory banks here, but think it allowed the missile to be powered but no coolant to flow until A/A mode was selected. This would save coolant, but would mean a few seconds for the seeker head to cool to operating temp.
COOL allowed coolant and power continuously and is what the switch was left in.
As an aside, there a 2 different coolant specifications for the AIM-9 family; USAF spec and USN. The major difference is where the coolant tank is located, and because of this the amount of coolant available. USN missiles (which we had on the A4) have the coolant in the missile rail and coolant is fed through the missile umbilical to the seeker. When the missile is fired, a one way valve traps coolant for continued seeker operation.
USAF missiles have the coolant in a smaller tank inside the sidewinder body - and this is the origin of the STBY position for the AIM-9 switch as it only uses coolant when required.
Great photos OJ. I had no idea that these panels and junctions were built in NZ.
|
|
|
Post by kiwiscanfly on Mar 16, 2010 1:35:02 GMT 12
The really scary thing is kiwiscanfly wasn't actually born then!! Yes very true but when you want to join the RNZAF it's good to know about the past and im am using the RNZAF history for some of my studies  As well as the fact that i knew the last bloke to fly the A4-K in 2001-2?? Sorry if my facts were a bit off- but it still seems to me that to finish the upgrades and then only get another 7-8 years out of them is a bit of a waste I feel the same way about the C-130 deal at the moment (waste)
|
|
|
Post by kiwiscanfly on Mar 16, 2010 1:37:37 GMT 12
oh and im not a tech expert.......... but taking DT for my IB level for my diploma and i must say its amazing to me how much was done by safeair and the RNZAF Avionics team......... great job looking at the pictures 
|
|
|
Post by b10m on Mar 16, 2010 20:09:13 GMT 12
It's STBY which we didn't use. Scratching the memory banks here, but think it allowed the missile to be powered but no coolant to flow until A/A mode was selected. This would save coolant, but would mean a few seconds for the seeker head to cool to operating temp. COOL allowed coolant and power continuously and is what the switch was left in. As an aside, there a 2 different coolant specifications for the AIM-9 family; USAF spec and USN. The major difference is where the coolant tank is located, and because of this the amount of coolant available. USN missiles (which we had on the A4) have the coolant in the missile rail and coolant is fed through the missile umbilical to the seeker. When the missile is fired, a one way valve traps coolant for continued seeker operation. USAF missiles have the coolant in a smaller tank inside the sidewinder body - and this is the origin of the STBY position for the AIM-9 switch as it only uses coolant when required. Great photos OJ. I had no idea that these panels and junctions were built in NZ. Thanks Barnsey, One more question, right hand end of the same unit is a switch with Arm/High/Safe/Low. What was that for.
|
|
|
Post by skyhawkdon on Mar 17, 2010 6:51:39 GMT 12
It's a 3-position switch (High/Safe/Low)for manually arming the high drag bombs when fitted. They could be dropped in either high or low drag configuration depending on the position of the switch.
I will need to check my notes, but I think this could also be selected through the NAS head down display as well?? Barnsey may remember.
|
|
|
Post by Barnsey on Mar 18, 2010 17:04:46 GMT 12
As Phil and Don have said!! The ARM switch is for bomb config, only when in manual bombs mode (as selected on the rotary switch on the right of the panel). Normally, the sequencing of the solenoids and fuze interface if using an electronic FMU-139 fuze is controlled by the Nav Attack System in AUTO. Here's picture of a selectable high drag bomb with the arming wires, which may make the nose and tail solenoid operation clearer: (from www.ordnance.org a great site!) 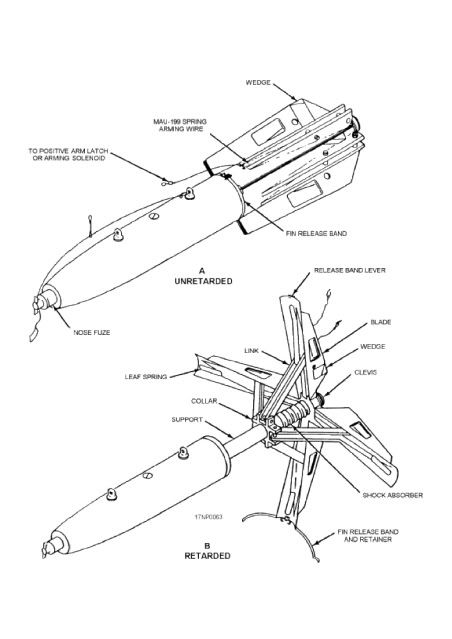 If dropping in HIGH, then both solenoids on the bomb rack will remain shut and hold the wires allowing the tail to open and the fuse propellor to spin and arm the bomb. in SAFE, then both solenoids open and the arming wires are not able to withdraw. This is same as if the Emergency Jettison or Selective Jettison handles are used in LOW, the nose solenoid stays shut to allow the nose fuze to spin up, but the tail opening wire is released. After dropping ordinance, the aircraft will return with the lengths of arming wire hanging from the weapons pylons. "Back in the good old days", with great people. God, I miss it!!! Cheers Phil
|
|
|
Post by skyhawkdon on Mar 18, 2010 18:01:42 GMT 12
quot;Back in the good old days", with great people. God, I miss it!!! Amen to that! Are you coming to the 75 Sqn Association reunion in Palmy in 2 weekends time Phil and Phil?
|
|
|
Post by Barnsey on Mar 18, 2010 18:02:19 GMT 12
Was it the tail arming wire that used to stay on the pylon, Phil? I'm sure I remember lengths of arming wire hanging from the pylon after HE trips... (it could be the psychotropic drugs however!)
|
|
|
Post by b10m on Mar 18, 2010 18:21:56 GMT 12
Thanks for that, Impressive stuff, to see all that wiring contained like that, and all the knowledge that goes with it. respect.
|
|
|
Post by phil on Mar 18, 2010 19:05:30 GMT 12
There were a number of different configurations as I recall, and some certainly left the wire behind, but due to the damage caused we tended to make sure the wires went with the bombs. If memory serves me there was a thinner black wire used on the FMU139, that may indeed have stayed with the aircraft.
Don, I've had just about as much as I can handle of the 75 SQN reunion already. We just about answer the phone '75 SQN association' at work at the moment! I'm not actually a member so most likely wont be there. Glen did ask if I could photograph the dinner, but I don't really have the right gear to do the job justice.
|
|
|
Post by yogi on Mar 26, 2010 21:13:43 GMT 12
those are great pics. Shows some seriously 'tidy' wiring work from some very skilled chaps.
|
|
|
Post by Calum on Mar 27, 2010 0:21:58 GMT 12
Here are some "Boxes" Junction Box ( Can't remember which one right now but we will find out ....  I hated having to change this one. IIRC it was on the floor under the instrument panel 
|
|
|
Post by Calum on Mar 27, 2010 0:27:58 GMT 12
The first Kahu prototype (NZ6254) flew on 2 June 1988 and the last production airframe (NZ6202) was delivered back to 75 Sqn in June 1991. 21 airframes were upgraded in 3 years, not a bad effort for a small RNZAF/Safe Air team! I'm sure the current C-130 and P-3 upgrade project teams are green with envy! With the certification stuff we have to deal with know , something like Kahu would never happen in that timeframe these days.
|
|