|
Post by Deleted on Nov 28, 2021 15:55:28 GMT 12
Inspired by you and David Glen I'm becoming increasingly curious about attempting a similar project with a P-40E. I'm immensely grateful to you for giving us these updates.
|
|
|
Post by nzgrasshopper on Nov 28, 2021 17:07:40 GMT 12
Inspired by you and David Glen I'm becoming increasingly curious about attempting a similar project with a P-40E. I'm immensely grateful to you for giving us these updates. Thanks Zac. It has turned into a much bigger project than I thought it would when I first started 15 years ago. For many years, I was only able to work on Gloria for 2 weeks out of 6, due to work. This has improved in the last few years, hence the progress on the rear fuselage. More than happy to share the progress and if you dive in happy to provide answers to any questions. Biggest choice is scale and how much detail - hence time you want to commit. Wooden frame overlaid with alloy and dummy rivets or full structural. I went with 1/6 as at the time there was a large amount of 1/6 scale diorama items being released. Realistic M2 BMG and accurate .50 cal ammo, etc. A lot of this was a limited run and is no longer available. 1/5 scale is more popular in the R/C community and there is a lot of scale items for cockpits etc. More so than 1/6. Luckily, 3D printing has developed over the years and this is making some items easier to create, V1710 engine etc. Which P40E are you thinking of replicating?
|
|
|
Post by planecrazy on Nov 28, 2021 20:54:20 GMT 12
Beginning of the fin assembly.   Sorry if this is a silly question the reason for using a mixture of brass and alloy?
|
|
|
Post by nzgrasshopper on Nov 28, 2021 22:30:07 GMT 12
Beginning of the fin assembly.   Sorry if this is a silly question the reason for using a mixture of brass and alloy? A mixture of convenience, strength and practicality. The top rudder hinge needs to be straight, I have found that even with a lot of care, aluminium still bends, even when 1.5 mm thick. There will also be some kind of bearing required, which will be more brass tube soldered onto the back of the rudder horn. The bottom section on the left of the rudder is part of the lower bearing section. There is one hinge assembly that attaches to the bottom of station 18 and another that attaches to the bottom of the fin. These fittings were a casting, that was then machined. At 1/6, this is far to complex, so I soldered brass sections together to make the same shape. K&S make tubing that is designed so one size slides into the next snugly, making good bearings. Aluminium, tends bind up, but the brass tube stays free. The trim tab faring would have been pressed I'm guessing. It was easier for me to put a rolled fold into brass sheet and solder this into a slotted piece of brass strip and them trim. The curved lower section of the rudder, I tried to make out of aluminium. It didn't work that well, so I flattened some brass tube that was curved to the required shape and soldered brass sheet to either side. I prefer to use aluminium where possible as the brass is harder to drill.
|
|
|
Post by nzgrasshopper on Dec 1, 2021 16:59:04 GMT 12
|
|
|
Post by nzgrasshopper on Dec 2, 2021 18:38:39 GMT 12
Fin skins with reinforcing. 
|
|
|
Post by planecrazy on Dec 3, 2021 20:02:11 GMT 12
Looking closely at those rivet jobs, wow there is some work putting them in! Noticed the small scratches, next silly question, have you cut and scratched yourself alot?
|
|
|
Post by Mustang51 on Dec 3, 2021 21:20:56 GMT 12
Getting countersunk rivets right full size is a real bear not to get snap marks........let alone at this scale
|
|
|
Post by nzgrasshopper on Dec 4, 2021 20:43:17 GMT 12
Looking closely at those rivet jobs, wow there is some work putting them in! Noticed the small scratches, next silly question, have you cut and scratched yourself alot? Touch wood, no major cuts or scratches so far. A few close calls though. Worst accident is the tip of a 1mm drill going into my thumb when using it as back pressure on odd shapes that can't be laid on a piece of wood instead.
|
|
|
Post by nzgrasshopper on Dec 4, 2021 20:51:23 GMT 12
Getting countersunk rivets right full size is a real bear not to get snap marks........let alone at this scale Mostly through good luck. From my limited knowledge of setting rivets properly on a full size aircraft, the bucking bar goes on the tail end and the rivet gun goes onto the head. Due to scale, lack of access and using a nail punch and small hammer, all of the rivets are set the other way round. The round head or flat of the countersunk head sits on a steel block and the tail is trimmed down and penned over. Biggest problem with the countersunk rivets is under or over sizing the countersunk hole. most of the time they sit flush, but sometimes the head sit pround of the skin and needs a slight touch of a file to smooth it out. A good coat of paint hides all manner of sins.
|
|
|
Post by Mustang51 on Dec 5, 2021 12:42:24 GMT 12
nzgrasshopper....my hat is off to you Sir !
|
|
|
Post by nzgrasshopper on Dec 17, 2021 19:41:41 GMT 12
Early stages of the horizontal stabiliser. 
|
|
|
Post by Mustang51 on Dec 17, 2021 21:59:47 GMT 12
Feel like a job assisting with a Birdog rebuild ?
|
|
|
Post by nzgrasshopper on Dec 18, 2021 8:44:54 GMT 12
Feel like a job assisting with a Birdog rebuild ? Thanks for the tempting offer. The procurement officer only tolerates one aviation endeavour at a time.
|
|
|
Post by nzgrasshopper on Dec 26, 2021 17:41:31 GMT 12
|
|
|
Post by nzgrasshopper on Dec 26, 2021 19:15:04 GMT 12
Top and bottom skins between webs 1 and 4 
|
|
|
Post by Dave Homewood on Dec 27, 2021 13:22:18 GMT 12
Stunning work. I love the updates!
|
|
|
Post by Deleted on Dec 28, 2021 15:19:40 GMT 12
Me too. Truly inspirational.
|
|
|
Post by nzgrasshopper on Dec 30, 2021 15:08:30 GMT 12
Slowly coming together. Top view of horizontal stabiliser.  Underside, lots of holes and rivets. 
|
|
|
Post by nzgrasshopper on Jan 1, 2022 20:06:16 GMT 12
Holiday break time being put to good use. All of the skin stiffeners have been made and the skin rivets drilled out. Just need to disassemble, paint inside, countersink external skins and then final rivet together. 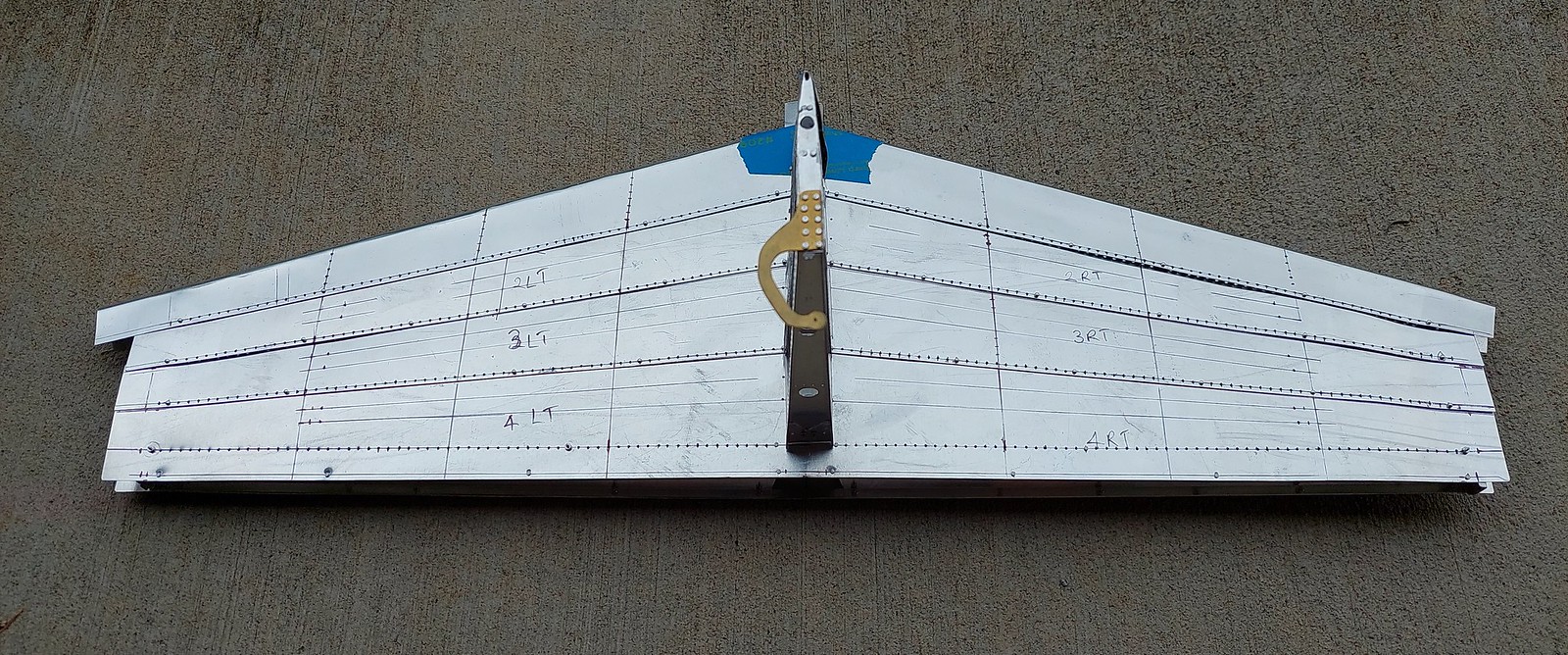  Next tricky step will be to make the connecting studs that hold the fin to the horizontal stabiliser and the horizontal stabiliser to the rear fuselage. 
|
|